HDI Multilayer Surface Mount PCB Assembly For Small Home Appliance
Place of Origin | Shenzhen |
---|---|
Brand Name | YScircuit |
Certification | ISO9001,UL,REACH, RoHS |
Model Number | YS-HDI-0010 |
Minimum Order Quantity | 1 piece |
Price | 0.04-5$/piece |
Packaging Details | Foam cotton + carton + strap |
Delivery Time | 2-8 days |
Payment Terms | T/T,PayPal, Alibaba pay |
Supply Ability | 251,000 square meter/year |
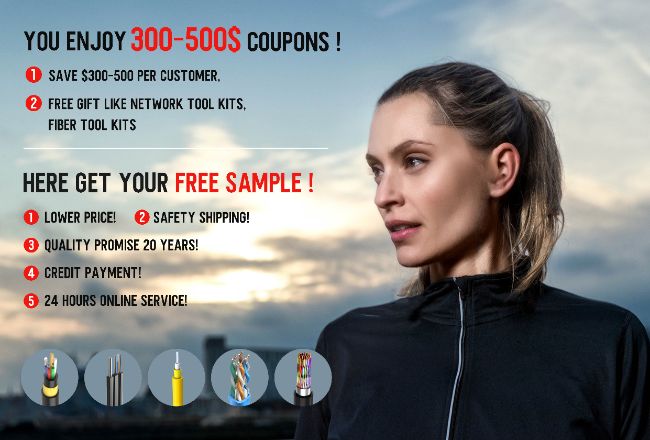
Contact me for free samples and coupons.
Whatsapp:0086 18588475571
Wechat: 0086 18588475571
Skype: sales10@aixton.com
If you have any concern, we provide 24-hour online help.
xMaterial | FR4 | Size | According To Customer Request |
---|---|---|---|
Process | Immersion Gold/sliver | Surface Finishing | HASL/HASL-LF |
Copper Thickness | 1oz | Base Material | FR-4 |
Min. Line Spacing | 0.25mm(10mil) | Board Thickness | 0.2-6.0mm |
High Light | Multilayer Surface Mount PCB Assembly,HDI Surface Mount PCB Assembly |
Custom Small Home Appliance Multilayer HDI PCB & PCBA Fabrication Manufacture SMT PCB Assembly
What is HDI PCB?
HDI stands for High Density Interconnector. A circuit board which has a higher wiring density per unit area as opposed to conventional board is called as HDI PCB. HDI PCBs have finer spaces and lines, minor vias and capture pads and higher connection pad density. It is helpful in enhancing electrical performance and reduction in weight and size of the equipment. HDI PCB is the better option for high-layer count and costly laminated boards.
Regarding the electrical needs of high-speed signal, the board should have various features i.e. high-frequency transmission capability, impedance control, decreases redundant radiation, etc. The board should be enhanced in the density because of the miniaturization and arrays of the electronic parts. In addition, to the result of the assembling techniques of leadless, fine pitch package and direct chip bonding, the board is even featured with exceptional high-density.
Innumerable benefits are associated with HDI PCB, like high speed, small size and high frequency. It is the primary part of portable computers, personal computers, and mobile phones. Currently, HDI PCB is extensively used in other end user products i.e. as MP3 players and game consoles, etc.
HDI PCBs take advantage of the most recent technologies existing to amplify the functionality of circuit boards by means of the similar or little amounts of area. This development in board technology is motivated by the tininess of parts and semiconductor packages that assist superior characteristics in innovative new products like touch screen tabs.
HDI PCBs are described by high-density features comprising of laser micro-vias, high performance thin materials and fine lines. The better density allows extra functions per unit area. These types of multifaceted structures give the required routing resolution for large pin-count chips which are used in mobile devices and other high technology products.
The placement of the parts on the circuit board needs extra precision than conservative board design due to miniature pads and fine pitch of the circuitry on the circuit board. Leadless chips require special soldering methods and additional steps in the assembly and repair process.
The lesser weight and size of the HDI circuitry means the PCBs fit into the little spaces and have a smaller amount of mass than conservative PCB designs. The smaller weight and size even signifies that there is lesser chance of harm from mechanical shocks.
HDI PCB:
High density interconnect PCB, are a way of making more room on your printed circuit board to make them more efficient and allow for faster transmission. It's relatively easy for most enterprising companies that are using printed circuit boards to see how this can benefit them.
Advantages of HDI PCB
The most common reason for using HDI technology is a significant increase in packaging density.
The space obtained by finer track structures is available for components.
Besides, overall space requirements are reduced will result in smaller board sizes and fewer layers.
Usually FPGA or BGA are available with 1mm or less spacing.
HDI technology makes routing and connection easy, especially when routing between pins.
Parameters
- Layers: 12
- Base Material:FR4 High Tg EM827
- Thickness:1.2±0.1mm
- Min.Hole Size:0.15mm
- Minimum Line Width/Space:0.075mm/0.075mm
- Minimum Clearance between Inner Layer PTH and Line: 0.2mm
- Size:101mm×55mm
- Aspect Ratio:8 : 1
- Surface treatment:ENIG
- Speciality: Laser via copper plated shut,VIPPO Technology,Blind Via and Buried Hole
- Applications:Telecommunication
YScircuit HDI PCB manufacturing capabilities overview | |
Feature | capabilities |
Layer Count | 4-60L |
Available HDI PCB Technology | 1+N+1 |
2+N+2 | |
3+N+3 | |
4+N+4 | |
5+N+5 | |
Any layer | |
Thickness | 0.3mm-6mm |
Minimum line Width and Space | 0.05mm/0.05mm(2mil/2mil) |
BGA PITCH | 0.35mm |
Min laser Drilled Size | 0.075mm(3nil) |
Min mechanical Drilled Size | 0.15mm(6mil) |
Aspect Ratio for laser hole | 0.9:1 |
Aspect Ratio for through hole | 16:1 |
Surface Finish | HASL, Lead free HASL,ENIG,Immersion Tin, OSP, Immersion Silver, Gold Finger, Electroplating Hard Gold, Selective OSP,ENEPIG.etc. |
Via Fill Option | The via is plated and filled with either conductive or non-conductive epoxy then capped and plated over |
Copper filled, silver filled | |
Laser via copper plated shut | |
Registration | ±4mil |
Solder Mask | Green, Red, Yellow, Blue, White, Black, Purple, Matte Black, Matte green.etc. |
layer/m² | S<1㎡ | S<3㎡ | S<6㎡ | S<10㎡ | S<13㎡ | S<16㎡ | S<20㎡ | S<30㎡ | S<40㎡ | S<50㎡ | S<65㎡ | S<85㎡ | S<100㎡ |
1L | 4wds | 6wds | 7wds | 7wds | 9wds | 9wds | 10wds | 10wds | 10wds | 12wds | 14wds | 15wds | 16wds |
2L | 4wds | 6wds | 9wds | 9wds | 11wds | 12wds | 13wds | 13wds | 15wds | 15wds | 15wds | 15wds | 18wds |
4L | 6wds | 8wds | 12wds | 12wds | 14wds | 14wds | 14wds | 14wds | 15wds | 20wds | 25wds | 25wds | 28wds |
6L | 7wds | 9wds | 13wds | 13wds | 17wds | 18wds | 20wds | 22wds | 24wds | 25wds | 26wds | 28wds | 30wds |
8L | 9wds | 12wds | 15wds | 18wds | 20wds | 20wds | 22wds | 24wds | 26wds | 27wds | 28wds | 30wds | 30wds |
10L | 10wds | 13wds | 17wds | 18wds | 20wds | 20wds | 22wds | 24wds | 26wds | 27wds | 28wds | 30wds | 30wds |
12L | 10wds | 15wds | 17wds | 18wds | 20wds | 20wds | 22wds | 24wds | 26wds | 27wds | 28wds | 30wds | 30wds |
14L | 10wds | 16wds | 17wds | 18wds | 20wds | 20wds | 22wds | 24wds | 26wds | 27wds | 28wds | 30wds | 30wds |
16L | 10wds | 16wds | 17wds | 18wds | 20wds | 20wds | 22wds | 24wds | 26wds | 27wds | 28wds | 30wds |
30wds |
FQA
What is HDI PCBs?
High density interconnect (HDI) PCBs represent one of the fastest-growing segments of the printed circuit board market.
Because of its higher circuitry density, the HDI PCB design can incorporate finer lines and spaces, smaller vias and capture pads, and higher connection pad densities.
A high-density PCB features blind and buried vias and often contains microvias that are .006 in diameter or even less.
1.Multi-step HDI enables the connection between any layers;
2.Cross-layer laser processing can enhance the quality level of multi-step HDI;
3.The combination of HDI and high-frequency materials, metal-based laminates, FPC and other special laminates and processes enable the needs of high density and high frequency, high heat conducting, or 3D assembly.